Plastics
With a long history, plastic was first introduced in the late 1800s. The discovery of this polymer of cellulose and cotton fibers that could be crafted into different shapes and sizes was revolutionary at the time. Then in 1907 the synthetic plastic was introduced. Many different industries use plastics such as the food and beverage industry, packaging, chemical plants, and construction just to name few. Later on in the 70s and 80s it became a growing concern of the environmental impact plastics were having on the environment. Currently, researchers are working on new ways to make plastic more renewable.
In the manufacturing of plastics, particulate from polymers, resins, fiber-reinforced plastic (FRP) and other can be a safety risk to workers.
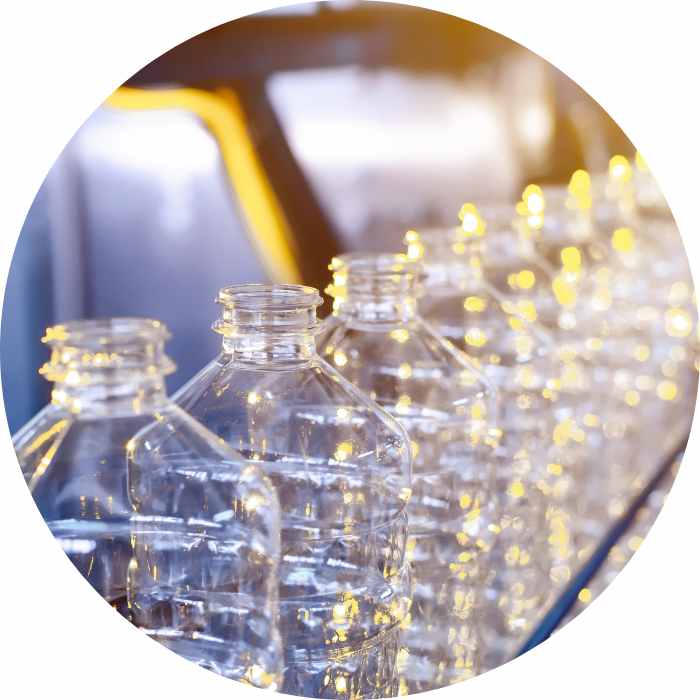
Various Processes
Much like other industries, there can be many different processes involved in plastics manufacturing. Things like injection molding, conveying, pelletizing, transporting, extrusion, and more. For example, if we were to show you how a plastic bottle is made, you would see that at any step in the process, there is potential for particulate and chemical dusts to be created.
First thousands of pellets are mixed together and then go through a process called injection molding. These pellets are melted down and molded into the bottle shape. In some instances this is done in many steps to create a more durable plastic. Sometimes extrusion molding is done instead of injection molding. In extrusion the plastics is heated and extrudes onto a conveyor and then clamped down into molds.
Sometimes the cutting and trimming of plastics is necessary to cut off excess. They can then be heat treated as well.
All throughout these processes workers can be exposed to harmful dust and chemical fumes.
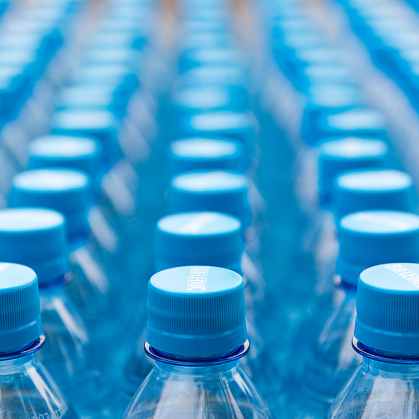
Dust Types
- Chemical Dusts
- Fiberglass
- PVC
- FRP
- Mineral
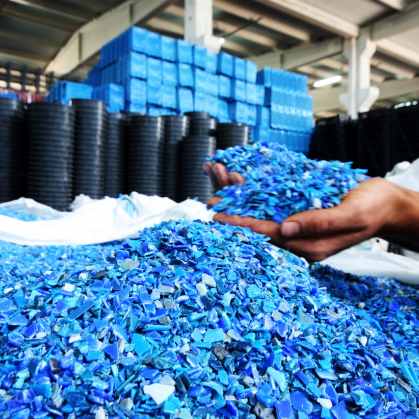
Health Risks
When workers are exposed to particulate and chemical fumes, they can be at risk for harmful health effects. Chemical fumes from sources such as PVC, styrene, phenol, and others can cause eye, nose, and skin irritation, lung damage, and other health issues. It is important to include control measures to reduce and control fumes and particulate to keep workers and the facility safe.
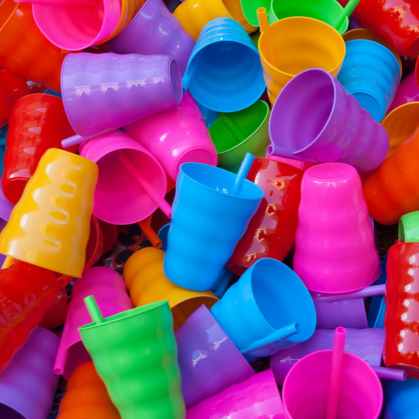
OSHA Regulations
The plastics industry is subjected to regulations just like any other industry. One of these being OSHA regulations. When dealing with "nuisance dusts", it is essential that safety is a #1 priority. Facilities must follow proper cleaning and housekeeping procedures as well as following Permissible Exposure Limits (PEL) setup by OSHA. The limit for nuisance dust is 5 mg/m3
Plastic manufacturers must also be aware of EPA (Environmental Protection Agency) rules when disposing of plastic waste.
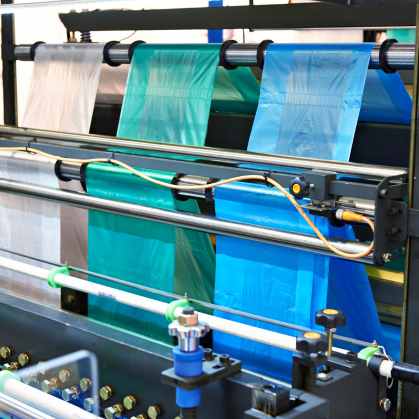
Combustible Dust Risks
A lot of dust generated in plastics is combustible. This means that it is extremely likely to combust when ignited by an ignition source. For example, extremely fine dusts generated in plastics manufacturing is highly combustible. Ignition sources can be a spark generated from equipment, electrostatic discharges, or even something as simple as a cigarette butt. That is why it is so important that work areas are kept clean and dust-free.
It is more than essential to protect workers, and manufacturing facilities from dust explosions. Once it ignites there is no stopping the explosive chain reaction. Implementing dust control and industrial air solutions is a good preventative measure.
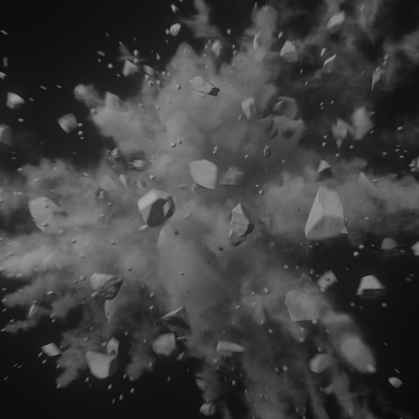